In performing sampling inspection, German Quality Control inspectors exclusively apply the ISO 2859-1, ANSI/ASQ Z1.4, MIL-STD105E standard and the tables provided by it. This document, published by the International Organization for Standardization- an essential guide used in quality control. When an inspector goes to your manufacturer to conduct a product quality inspection, they use AQL & Sample Size standards to understand how many units he should inspect in one shipment and the maximum number of defective products are accepted. This is a more cost-effective approach and is widely accepted for most consumer goods.
What is AQL?
‘AQL‘ stands for ‘Acceptance Quality Limit‘, and is defined as the “quality level that is the worst tolerable”. It represents the maximum number and type of defects that can be accepted in an inspected example, beyond which the entire batch must be rejected. Based on the sampling data, the customer can make an informed decision to accept or reject the lot. Your inspection report will clearly state whether your production has passed or failed your selected Acceptable Quality Tolerance level.
AQLs can be set for a level or number of critical, major and minor defects. In practice, three levels of defects are often used for consumer products:
Critical Defects – 0%
Not acceptable if a product can be harmful to a user, it is not compliant with regulations, or the defect results in product failure.
Major Defects – 2.5%
The product won’t be considered acceptable by the end-user
Minor Defects – 4.0%
Failure to meet the specification in ways that most buyers would still accept.
This AQL percentage is used mostly during Pre-shipment inspection (when the products are ready to be shipped out), and sometimes during production (when the number of products is sufficient to have an idea of the batch’s average quality).
AQL Table
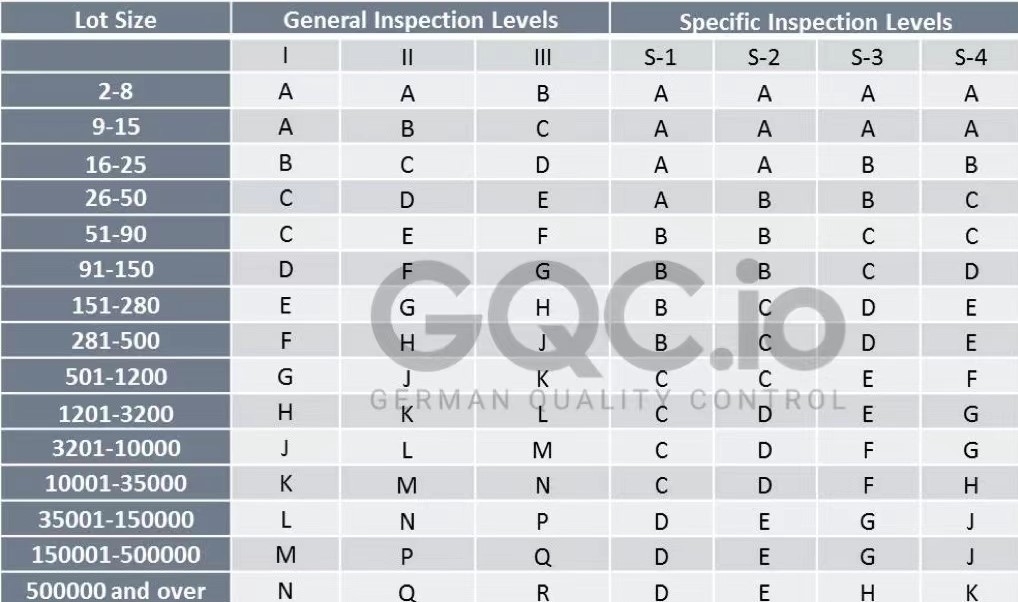
The most common AQL standard for the consumer goods industry was developed by the American National Standards Institute (ANSI), that is why sometimes it is called the “ANSI” table. There are three main parameters: the lot size, the inspection level, and the AQL limits.
The lot size is the quantity of all products. If you order different products, consider each product as a separate lot. As for the inspection level, a different product will require a different level of inspection. There are normal inspection and special inspection levels. The AQL limits should be appropriate for your market. If your customers accept very few defects, you might want to set a lower AQL for both major and minor defects.
You can use AQL calculator, which will automatically show all the information, but it is good to understand how to read the tables.
Examples:
For a hypothetical inspection of production with 3,500 units, the client selected level II normal inspection and AQL of 2.5Maj/4.0Min
You can see in Table 1, the intersection of the respective Lot Size and General Inspection Level indicates sample size code letter L. Then, in Table 2, we locate row L, which indicates the required sample size of 200. To comply with AQL 2.5 and 4.0, not more than 10 major defects or 14 minor defects are allowed in order to pass the inspection.
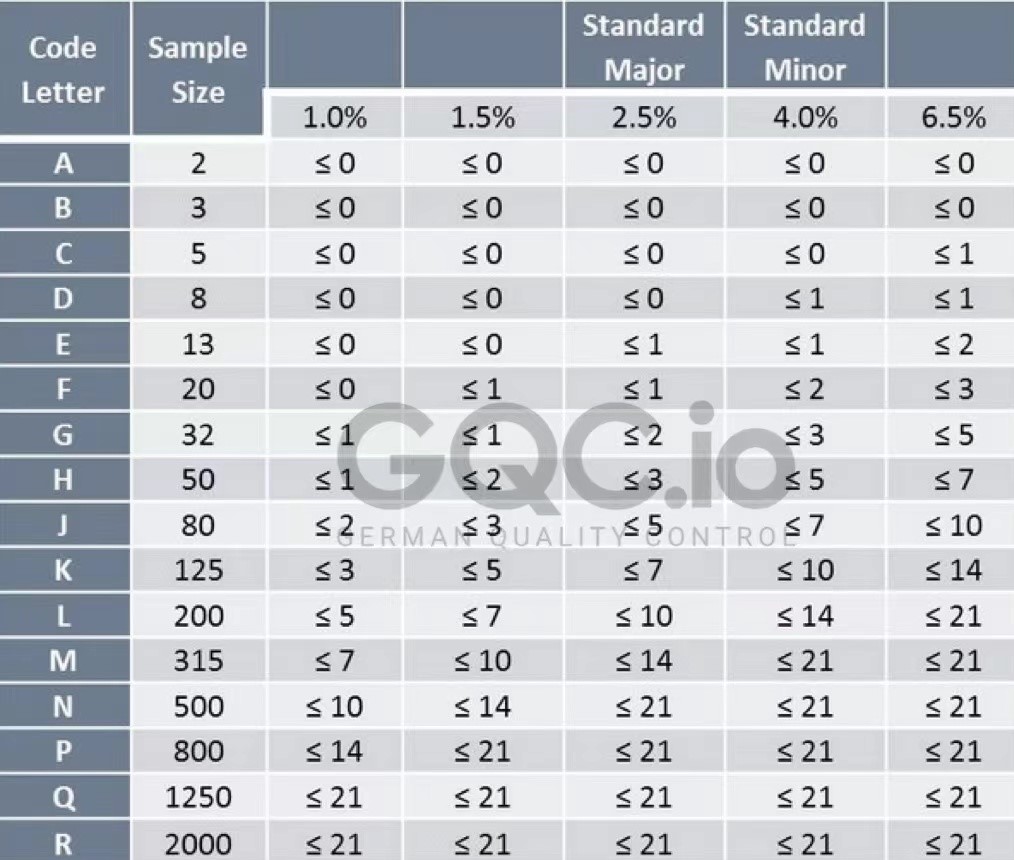
During quality inspection finding the number of defective products is only one part of an inspector’s job. Other imports parts are usually mentioned on the inspector’s checklist, which typically includes:
Packaging check (barcodes, inner packing, cartons, shipping marks).
Product check (aspect, workmanship, dimension, and other details)
Function and Safety test (Full function check according the product specifications and ensuring the end-user safety)
Specific tests defined in the inspection checklist (they might not be performed on all inspected samples if they are time-consuming or destructive)
General Inspection Levels
There are three General Inspection Levels — I, II, and III. The level you choose is the main factor that determines the number of goods an inspector will check. Sometimes, inspecting fewer units (Level I) can reduce costs since the inspection takes less time. This level is only a good choice if you trust your manufacturer and have a big quantity of goods. On the other hand, if you just started to work with a new factory and care about the quality, it is a good call to choose level III. An inspection with a larger sample size will take more time but will give you a better understanding of your product’s quality.
Special Inspection Levels
There are four Special Inspection Levels — S-1, S-2, S-3, and S-4. Using the Special levels will give you a smaller sample size. The results are not likely to differ significantly between units inspected and usually include the inspection of fewer than 10 units. Special Inspection is usually performed if your product requires time-consuming or technical tests, which might destroy your product.
AQL is a proven statistical model that has been used successfully for decades. It has broad adoption across the quality control industry. However, it’s important to remember that conducting an AQL inspection will not guarantee a defect-free order, as this is not its purpose. For more information, contact our team or book a free consultation.